Aluminum Circle Supplier: Choosing the Best Provider for Your Needs
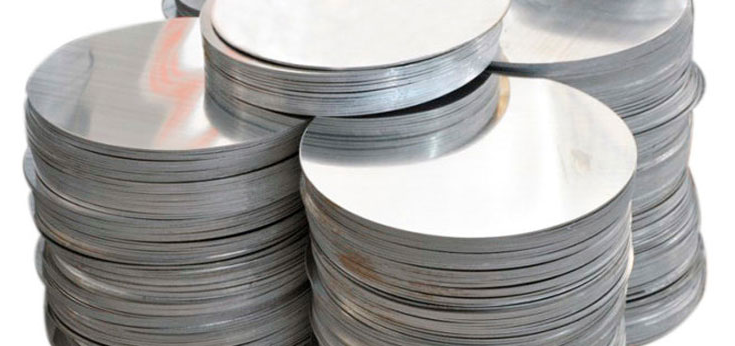
Introduction: Understanding the Role of Aluminum Circles in Industry
Aluminum circles are fundamental materials used in various industries, especially cookware, lighting, and electrical applications. These flat, round aluminum pieces offer flexibility, durability, and excellent thermal properties, making them ideal for creating a wide range of products, from cooking pots and pans to industrial and automotive parts. For manufacturers relying on aluminum circles, partnering with a trusted aluminum circle supplier ensures product quality, reliability, and cost-effectiveness.
This article provides an in-depth look at aluminum circle suppliers, exploring the manufacturing process, benefits of aluminum circles, key industries they serve, and factors to consider when selecting the right supplier.
What are Aluminum Circles?
Aluminum circles, also referred to as aluminum discs or blanks, are flat, circular pieces made from aluminum sheet materials. They can vary widely in thickness, diameter, and alloy composition, depending on their intended application.
Key Properties of Aluminum Circles
Aluminum circles are prized for several properties:
- Lightweight: Aluminum’s density is only one-third that of steel, making it highly sought after for lightweight applications.
- Excellent Conductivity: Aluminum is a great conductor of both heat and electricity, ideal for cookware and electrical components.
- Corrosion Resistance: The natural formation of an oxide layer protects aluminum from rust, extending its lifespan even in challenging environments.
- Strength and Malleability: Aluminum alloys offer an excellent balance of strength and malleability, making them easy to shape and durable for a variety of uses.
The Aluminum Circle Manufacturing Process
Aluminum circles undergo a specialized manufacturing process to ensure they meet specific standards and specifications. This process usually involves several key stages:
1. Material Selection
The process begins by selecting the appropriate alloy based on the desired properties for the end application. Common alloys include 1050, 1060, 3003, and 5052, each of which offers different levels of strength, corrosion resistance, and malleability.
2. Casting and Rolling
Raw aluminum or recycled aluminum is melted down, then cast into slabs. These slabs are rolled at high temperatures to reduce thickness and refine their structure, ultimately forming aluminum sheets.
3. Stamping or Blanking
Once the aluminum sheet has reached the desired thickness, it’s cut into circular shapes through stamping or blanking. This process involves using specialized presses and dies to produce precise, consistent circles without deforming the material.
4. Annealing
After stamping, the aluminum circles may be annealed to soften the material, relieving any internal stresses and improving flexibility. This process ensures the circles can be easily shaped during subsequent manufacturing steps, such as deep drawing.
5. Quality Control and Inspection
Before shipping, the aluminum circles are inspected for dimensional accuracy, thickness uniformity, and surface finish. Reputable suppliers implement strict quality control processes to ensure their products meet industry standards and client specifications.
Read also: Action Coach: Empowering Businesses to Achieve Growth and Success
Types of Aluminum Circles Available from Suppliers
Aluminum circle suppliers typically offer a wide range of options tailored to various industries and applications. Here are some common types of aluminum circles based on alloy and treatment:
- 1050 and 1060 Aluminum Circles: Known for high purity and excellent corrosion resistance, these alloys are typically used in cookware and electrical applications.
- 3003 Aluminum Circle: Containing manganese, 3003 offers superior corrosion resistance and is highly formable, making it ideal for cookware and kitchen utensils.
- 5052 Aluminum Circle: This alloy is stronger than 1050 and 3003, with excellent corrosion resistance, making it suitable for applications in marine and industrial settings.
- 6061 and 7075 Aluminum Circles: These high-strength alloys are often used in aerospace, automotive, and structural applications due to their durability and resistance to wear.
Each alloy type is selected based on its intended use, with some suited for cookware due to high thermal conductivity and others for structural applications requiring high strength.
Key Applications of Aluminum Circles Across Industries
Aluminum circles serve as critical components in various industries, where their unique properties help create durable, efficient products. Here are a few common applications:
1. Cookware and Kitchen Utensils
Aluminum’s heat conductivity makes it ideal for cookware, including frying pans, pots, and kettles. Aluminum circles are also used to create lids, baking trays, and other kitchen utensils due to their lightweight and corrosion-resistant properties.
2. Automotive Industry
In the automotive industry, aluminum circles are often used in creating lightweight components that enhance fuel efficiency. They’re used in parts like brake discs, fuel tanks, and heat shields, helping reduce vehicle weight and improve overall performance.
3. Lighting and Reflectors
Aluminum circles are commonly used in lighting applications, such as reflector dishes, due to their reflective qualities and durability. They’re ideal for applications requiring good thermal management, like LED lighting fixtures.
4. Aerospace
Aerospace applications demand high-strength materials with low weight, and certain aluminum alloys are ideal for this purpose. Aluminum circles are used in a variety of components, including parts for aircraft interiors and structural elements.
5. Electrical Applications
Aluminum circles are widely used in electrical applications due to aluminum’s conductivity. They are found in cable shielding, wiring, and conductive components where heat dissipation is essential.
6. Packaging
Aluminum circles are used in the production of various packaging materials, such as lids for food containers and can ends. Aluminum’s non-toxic nature, combined with its lightweight and recyclable properties, makes it a sustainable choice for packaging.
Conclusion: Finding the Right Aluminum Circle Supplier
Choosing the right aluminum circle supplier is a critical decision that can impact product quality, project timelines, and budget. Reliable suppliers provide high-quality aluminum circles tailored to meet the needs of various industries, from cookware to aerospace. When selecting a supplier, consider factors such as product quality, customization options, production capacity, and sustainable practices.
Partnering with a reputable aluminum circle supplier ensures consistent quality, timely delivery, and access to expert technical support, helping companies succeed in their projects. Aluminum circles continue to play a vital role across industries, and with the right supplier, companies can achieve exceptional results while meeting their sustainability goals.