Practices for Extending the Life of a Motor Winding Equipment
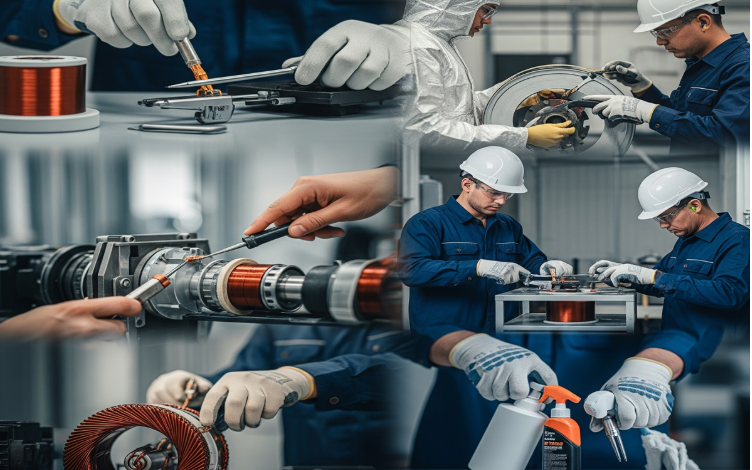
Motor winding equipment is vital in converting electrical energy into mechanical energy for various machines. Its durability directly influences motor performance and operational reliability. Extending winding life lowers maintenance costs and prevents unexpected downtime. Maintaining winding machine health is therefore crucial in industrial settings.
A combination of good maintenance practices and proper handling can significantly prolong winding life. This article outlines key practices that help maintain winding equipment in optimal condition. By following these guidelines, equipment longevity and efficiency can be maximized. These steps also improve safety and reduce repair expenses.
Regular Inspection
Regular inspection of motor winding equipment is essential to detect early signs of damage or insulation wear. Visual examination helps identify discoloration, cracks, or contamination on winding surfaces. Electrical tests like insulation resistance checks provide deeper insight into winding health. These inspections ensure timely identification of faults.
Carrying out inspections on a consistent schedule supports proactive maintenance. Detecting problems early prevents costly breakdowns and extends equipment life. Proper documentation of inspection results aids in tracking winding conditions over time. This approach enhances operational reliability and safety.
Proper Cleaning
Accumulated dust and dirt increase thermal resistance, causing heat buildup in windings. Cleaning motor winding equipment with gentle methods such as vacuuming or blowing with compressed air is effective. Harsh chemicals should be avoided as they may damage insulation. Keeping windings clean promotes better heat dissipation.
Regular cleaning reduces the risk of electrical shorts from conductive particles. It also helps prevent moisture retention on winding surfaces. Well-maintained winding equipment performs efficiently and lasts longer. Clean equipment contributes to reduced downtime and maintenance needs.
Temperature Control
Temperature is a critical factor affecting insulation lifespan in motor winding equipment. Excess heat accelerates degradation and weakens insulation materials. Using temperature sensors during operation helps monitor winding temperature. Proper cooling systems prevent overheating and thermal damage.
Maintaining operating temperatures within design limits is necessary for winding durability. Avoiding overloading and ensuring airflow can control excessive heat generation. Thermal management preserves insulation properties and motor reliability. Controlling temperature directly impacts winding longevity.
Moisture Prevention
Moisture reduces insulation resistance and promotes corrosion inside motor winding equipment. Sealing enclosures and using desiccant breathers prevent moisture ingress. In humid environments, periodic drying or heating helps keep windings dry. Preventing moisture accumulation protects winding insulation integrity.
Moisture-related insulation failure leads to electrical faults and costly repairs. Ensuring a dry operating environment extends motor service life. Maintenance practices must focus on moisture control to avoid breakdowns. Proper moisture prevention safeguards winding reliability.
Correct Storage
Motors stored improperly face risks of moisture damage, corrosion, and contamination. Storage areas should be dry, clean, and free from corrosive agents. Elevating motors off the ground and covering them reduces exposure to dirt and humidity. Proper storage preserves insulation and winding condition.
Long-term storage without protection leads to insulation deterioration. Maintaining environmental controls during storage keeps motors ready for use. Good storage practices minimize repair needs after idle periods. This ensures motors remain functional when needed.
Handling Care
Motor winding equipment is delicate and requires careful handling during transport and installation. Rough handling can cause winding displacement or insulation damage. Using proper lifting equipment and following guidelines minimizes risks. Training personnel in handling procedures is important.
Avoiding mechanical shocks prevents internal winding faults. Proper care reduces premature failures and improves equipment life. Handling protocols support safety and equipment longevity. Careful handling ensures motor reliability.
Quality Materials
The durability of motor winding equipment heavily depends on the quality of materials used. High-grade insulation, conductors, and varnishes withstand heat and mechanical stress better. Using quality materials during manufacturing or repairs ensures longer life. Inferior components accelerate degradation and failures.
Investing in premium materials reduces maintenance frequency and costs. Reliable components enhance motor efficiency and durability. Choosing the right materials is a foundational step in winding longevity. Quality directly translates to performance and lifespan.
Routine Testing
Periodic electrical testing is a key to monitoring winding health and insulation integrity. Insulation resistance and polarization index tests reveal aging or moisture presence. Surge comparison tests detect winding faults such as shorts or open circuits. Scheduling tests at intervals supports condition-based maintenance.
Routine testing prevents unexpected failures by detecting problems early. It provides data for informed maintenance decisions and repair planning. Maintaining detailed test records aids trend analysis and lifespan prediction. Regular testing improves motor reliability and safety.
Proper Loading
Operating motors within their rated load prevents excessive current and overheating. Overloading causes thermal stress that rapidly degrades winding insulation. Adhering to manufacturer load specifications protects winding integrity. Proper loading ensures efficient, safe motor operation.
Overload protective devices further prevent damage during abnormal conditions. Maintaining load balance reduces mechanical and thermal stresses on windings. Correct loading practices extend winding life and reduce failure risks. Avoiding overloading is essential for longevity.
Balanced Voltage
Voltage imbalance causes uneven heating and current distribution in motor windings. This localized overheating weakens insulation and shortens winding life. Monitoring supply voltage and correcting imbalances is necessary for winding health. Maintaining balanced voltage prevents premature failure.
Ensuring stable and symmetrical voltage supply supports uniform motor performance. Addressing supply irregularities protects insulation from thermal damage. Balanced voltage reduces mechanical stresses and promotes longevity. Electrical stability is especially important when operating precision equipment like a bldc motor winding machine, where consistent performance is critical for quality results.
Adequate Cooling
Effective cooling removes heat generated by motor operation, preserving winding insulation. Cooling methods include fans, air circulation, or liquid cooling, depending on motor design. Regular maintenance of cooling components prevents blockages and failures. Proper cooling keeps winding temperatures within safe limits.
Inadequate cooling leads to insulation breakdown and motor overheating. Ensuring cooling efficiency prolongs motor and winding lifespan. Temperature control through cooling is vital for reliability. Cooling system upkeep is an ongoing necessity.
Vibration Control
Excessive vibration causes mechanical fatigue that damages motor winding equipment insulation and conductors. Vibration arises from misalignment, imbalance, or external mechanical sources. Controlling vibration with proper mounting, alignment, and dampers protects motor integrity. Regular vibration monitoring detects early issues.
Reducing vibration minimizes mechanical stresses and insulation wear. Stable operation ensures longer winding life and motor reliability. Vibration control is an essential part of preventive maintenance. Addressing vibration early avoids costly repairs.
Avoiding Contamination
Contaminants like dust, metal particles, and chemicals degrade winding insulation. Sealed motor enclosures and controlled environments reduce contamination risks. Regular cleaning removes accumulated foreign matter that could cause electrical faults. Preventing contamination maintains winding performance.
Foreign material can create conductive paths leading to shorts or insulation failure. Keeping the environment clean protects winding insulation from damage. Contamination control extends motor service life and efficiency. Proper sealing and cleanliness are critical practices.
Timely Repairs
Prompt repair of winding damage prevents escalation into major failures. Delaying repairs often results in more extensive damage and higher costs. Addressing insulation cracks, varnish degradation, and conductor faults maintains motor health. Timely intervention supports continuous motor operation.
Qualified technicians should perform repairs using quality materials to restore winding integrity. Preventive repairs reduce unexpected downtime and extend equipment life. Staying proactive with repairs improves motor reliability. Repair timing is key for winding preservation.
Monitoring Operation
Continuous monitoring of current, voltage, temperature, and vibration gives real-time insight into motor health. Advanced systems can alert operators to abnormal conditions for quick response. Monitoring supports predictive maintenance and early fault detection. Data-driven operation extends winding lifespan.
Operational monitoring improves safety and reduces unplanned downtime. Keeping detailed records helps identify trends and plan maintenance activities. Effective monitoring maximizes motor performance and winding durability. It is a cornerstone of modern maintenance practices.
Honest Automation: Built to Last
Honest Automation is a trusted name in the manufacturing and supply of high-quality industrial solutions, specializing in durable and efficient motor winding equipment. With a strong foundation in engineering and years of hands-on experience, the company is committed to delivering products that meet the highest standards of performance and reliability across diverse applications and industries.
Focused on long-term value and customer satisfaction, Honest Automation offers comprehensive support from product consultation to after-sales service. Whether you’re looking for standard equipment or customized solutions, the team is dedicated to helping clients achieve lasting operational success. For more information or to connect with their specialists, please use the contact details below.
Phone: +86 189 2373 2990
Email: sales@honest-hls.com
Website: https://www.honest-hls.com/
Final Verdict
Extending motor winding equipment life requires combined efforts in inspection, cleaning, and temperature control. Preventing moisture ingress, handling motors carefully, and using quality materials are also essential. Routine testing, proper loading, balanced voltage, and cooling maintain optimal conditions. Vibration control, contamination avoidance, and timely repairs further support winding longevity.
Continuous operational monitoring enables proactive maintenance and early fault correction. Adopting these best practices reduces failures, lowers costs, and improves equipment reliability. Ultimately, these strategies ensure winding equipment performs efficiently and lasts longer in demanding applications.